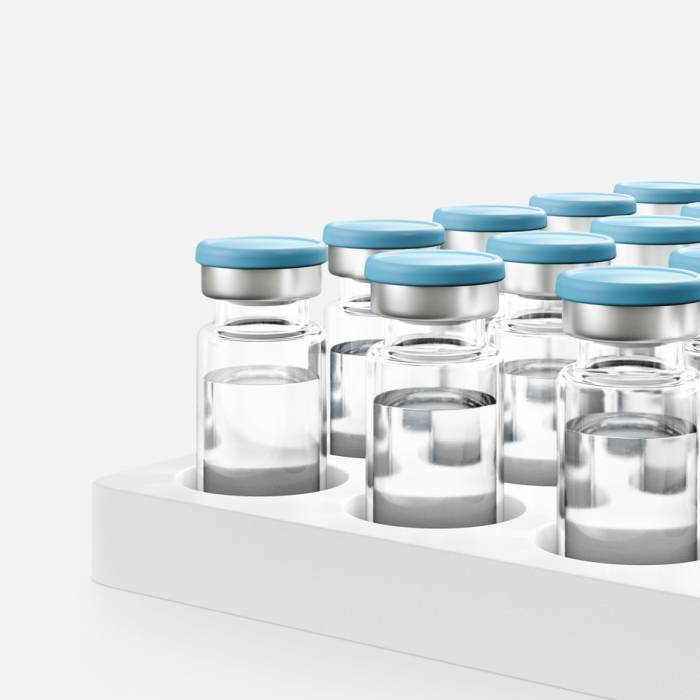

StarterPack™
Packaging & sterilization
Our service offering.
Lab testing to assure conformance with regulatory and industry requirements.
Datwyler’s lab service begins with assisting in compound selection through questionnaires to specify the requirements for the customer’s ideal product. Thanks to extensive product knowledge and experience, Datwyler’s R&D team is able to recommend the ideal compound solution aligned with the indicated requirements.
Pharmacopoeia and normative testing
Customized E.P.3.2.9 / USP<381> functional testing for injection stoppers
Normal and customized functional testing for infusion stoppers as per ISO8536-2
ICP – Elemental impurities as per ICH Q3D
Functionality
testing
Fitting test, part 2: popping up / off test
RSF – Residual Seal Force
Gliding profile testing for prefilled syringes and cartridges
Container Closure Integrity testing
PBSI – Plunger Barrel Seal Integrity test using He-leak testing
CCSI – Container Closure Seal Integrity test using laser-based headspace analyzer
CCSI – Container Closure Seal Integrity test using He-leak testing
Other standard industry testing
Extractables and leachables services
Moisture percentage of products
And others
Full support for your regulatory requirements.
Strict regulatory requirements
Comprehensive reports
Customized testing

Custom product design to make individual ideas become reality.
The co-engineering process incorporates three main phases.
Product Design
Product Analysis
Customized Engineering Activities
Finite Element Analysis to eliminate possible issues at an early stage in product development.
We increasingly employ numerical simulation techniques to ensure the best product functionality as well as efficient and reliable production processes at the core of our customer applications. We use Finite Element Analysis (FEA) to fully comprehend the functionality of new elastomer components before real prototypes exist. FEA permits the assessment of a wide variety of engineering problems ranging from structural mechanical analyses to mold flow investigations and facilitates the examination of parameters such as deformation, reaction forces, contact pressure, material stress, filling behavior, and temperature. Our customers benefit from an accelerated development cycle as well as superior product quality.
Industry-leading simulation capabilities in four areas.
At Datwyler, we offer industry-leading simulation capabilities, which serve as the basis for the best product performance and reliable serial production:
Testing & Modeling
Computer Aided Design (CAD)
Structural Mechanics
Mold Flow
Business continuity plans minimizing the risks for our customers.
At Datwyler, we take every measure to ensure our customers have access to their products, and we have a plan in place to mitigate supply risks. Our risk mitigation strategies consider disaster risks, product discontinuity, as well as regional supply constraints. By analyzing each of these areas in conjunction with our customers’ supply needs, we are able to develop a joint business continuity plan to assure security of supply of our customers’ products.